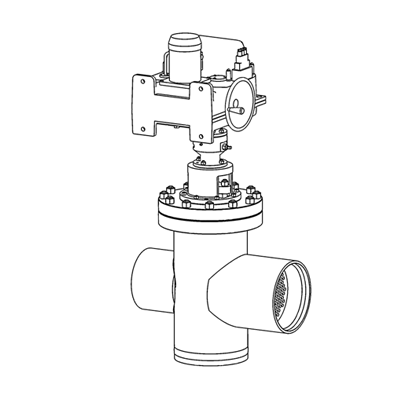
LRV regulating disk valves are designed and manufactured for custom-made operational conditions and parameters. According to the customer’s specification and depending on thermohydraulic calculations, the required flow characteristics are set, and, if needed, a multi-stage pressure reduction system is used (that allows for reduction of wear and tear of the valve spool, its noise and vibration); discharge is provided for significant pressure drops; anti-cavitation plugs and auxiliary throttling devices are provided for regulators of hot-water pipelines.